Excavators are essential machines in industries such as construction, mining, and roadwork, carrying out heavy tasks. However, after extended periods of high-intensity use, excavators inevitably develop faults and issues. To ensure construction progress and operational safety, it’s crucial to assess whether to repair or replace an excavator when it encounters significant problems. This article explores how to determine when it is time to replace an excavator due to serious issues.
1. Severe Engine Damage
The engine is the core component of an excavador. Once the engine suffers significant damage, it can result in the machine failing to start or operate correctly. Common engine issues include connecting rod failure, cylinder damage, and overheating leading to structural deformation. These problems are costly to repair, and even after repairs, the machine’s performance and lifespan are often significantly reduced. Therefore, if the engine cannot be repaired or the repair cost is too high, replacing the excavator is generally the best option.
2. Complete Hydraulic System Failure
The hydraulic system is a critical part of an excavator, responsible for driving the machine’s working components. If the hydraulic pump, motor, or valve assembly is severely damaged, repairs can be difficult and expensive, often requiring the replacement of many parts. Hydraulic system failure not only impacts the excavator’s normal operation but can also pose safety risks. Thus, if the hydraulic system experiences complete failure and the repair cost is prohibitive, replacing the excavator is more economical.
3. Severe Damage to the Chassis and Main Structure
The chassis and undercarriage of an excavator are the foundational structures that support the entire machine. If these parts suffer severe deformation or cracks, the stability and safety of the machine are greatly compromised. Repairing the chassis and main structure is often a labor-intensive process and may not restore the machine’s original performance. If these components are irreparably damaged, continuing to use the excavator poses significant safety risks. Therefore, when the chassis or main structure is severely damaged, replacing the excavator is a safer and more rational choice.
4. Severe Damage to the Track or Wheel System
The track or wheel drive system is responsible for the excavator’s mobility. With extended use under heavy loads, tracks or wheels may experience significant wear and damage. If the damage is severe and repairing it proves difficult or too expensive, replacing the entire machine becomes a more cost-effective option. This is particularly true for older machines, where repair costs are often hard to justify compared to purchasing a new excavator.
5. Complete Failure of the Electrical Control System
Modern excavators rely on an electrical control system to manage various work modes and operations. If the electrical control system fails completely, preventing the machine from operating correctly or impacting its precision, repairs may require replacing many electronic components and sensors. Electrical control system failure not only involves high repair costs but also affects the machine’s operational capabilities. Therefore, when the electrical system fails completely, and repairs are costly and difficult, replacing the excavator is often the best solution.
6. Long-Term Overuse or Severe Aging
Long-term overuse accelerates the aging of an excavator’s components, from the engine to the hydraulic system and chassis. When an excavator has been in use for over 10-15 years, and the components have been heavily worn due to extended heavy-duty operation, repairs may no longer restore the machine to its original performance. At this point, continued use of the old equipment can result in high repair costs and low efficiency. In such cases, replacing the machine with a new one is a more economical and reliable option.
7. Frequent Major Failures
If an excavator experiences frequent major failures, it can significantly impact construction schedules and lead to unnecessary repair costs. Repairing recurrent failures often involves replacing a large number of parts, and the costs of such repairs can rise substantially over time. Accumulated repair costs may eventually equal or exceed the cost of purchasing a new machine. In such cases, replacing the excavator with a new one is more economical and ensures smooth work progress.
Conclusion
As heavy-duty equipment, excavators are subject to wear and tear over time. When significant damage occurs, and repair costs are high or the machine’s performance cannot be restored after repair, replacing the excavator is often the most reasonable choice. Key factors to consider include engine failure, hydraulic system issues, chassis damage, electrical control system failure, and frequent major malfunctions. If the machine is aging significantly or frequently failing, evaluating the cost-effectiveness and safety of replacing it with a new excavator is the best approach to ensure efficiency and safety in construction operations.
Juemeng has over 15 years of experience in the international trade of high-quality used excavators. We specialize in offering a wide range of well-known brands, including Caterpillar, Komatsu, Hitachi, KOBELCO, and more. Our machines are in excellent condition with original parts, low hours, and thorough testing. We provide competitive pricing and aim to establish long-term partnerships with customers worldwide. Additionally, we offer after-sales service, including free test drives, ensuring customer satisfaction. If you are interested in second-hand excavators, please contact us.
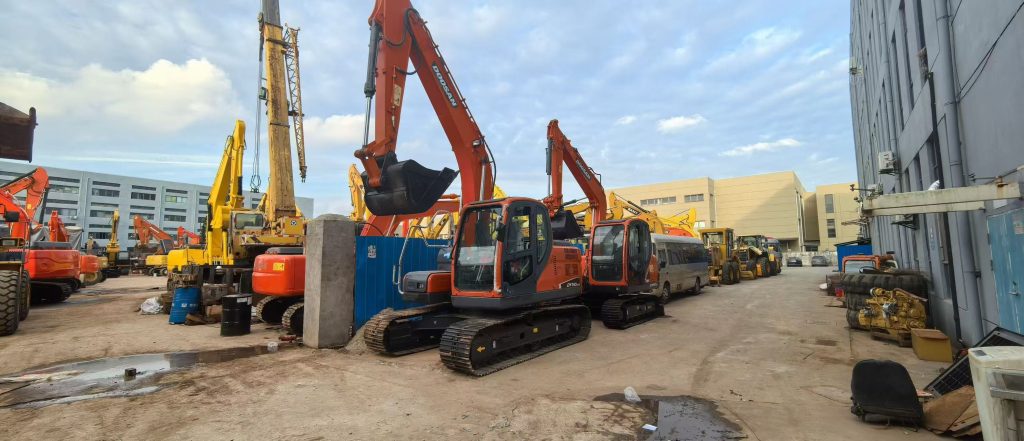
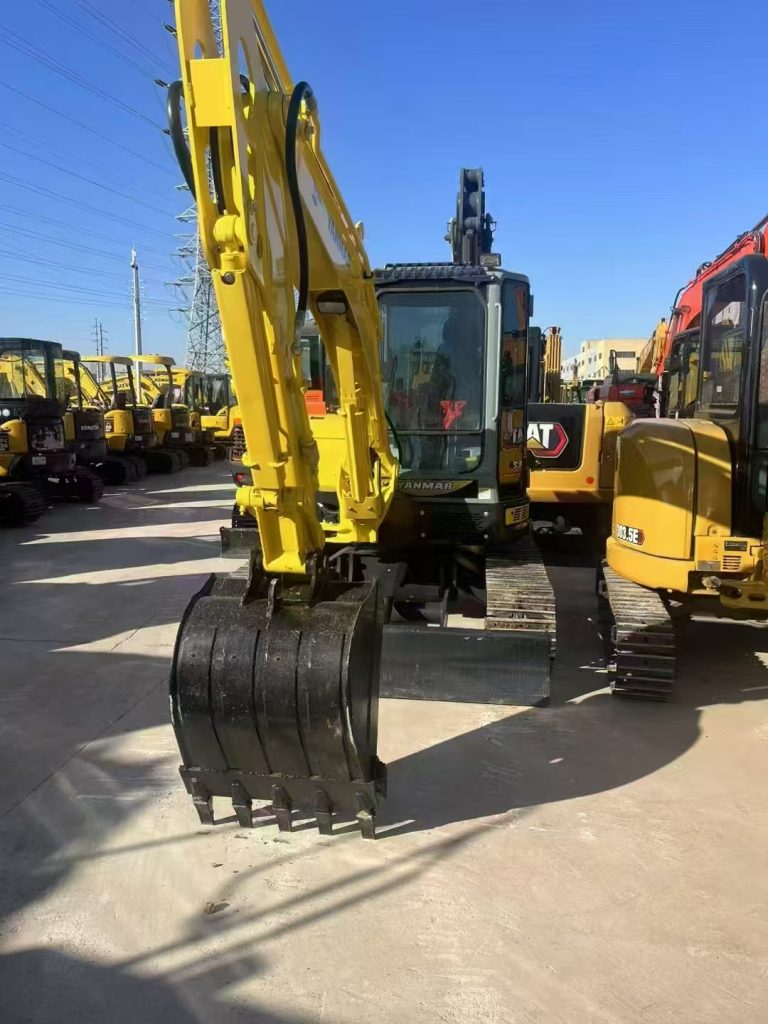
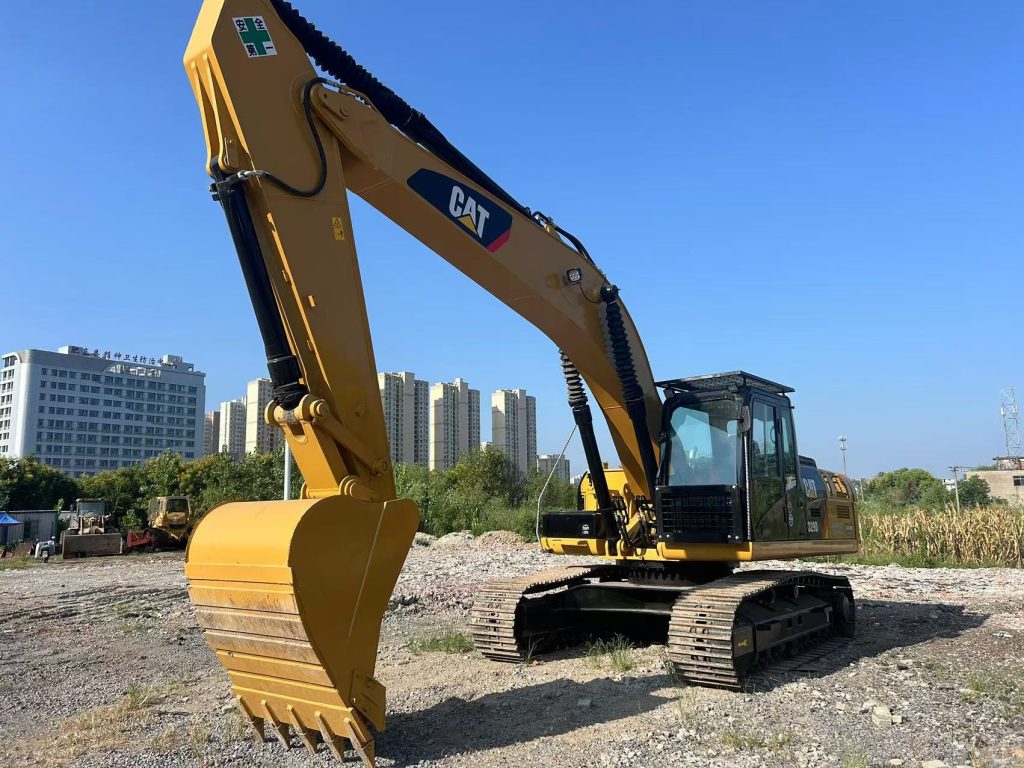